Anti-Glare Coating
Applying Glass Anti-Glare Coating involves cleaning the glass, depositing a specialized anti-glare material, curing the coating, and conducting quality control checks. This process aims to reduce reflections and enhance visibility on glass surfaces. NWG's AG Coating line has both Chemical Etching and Spraying process methods.
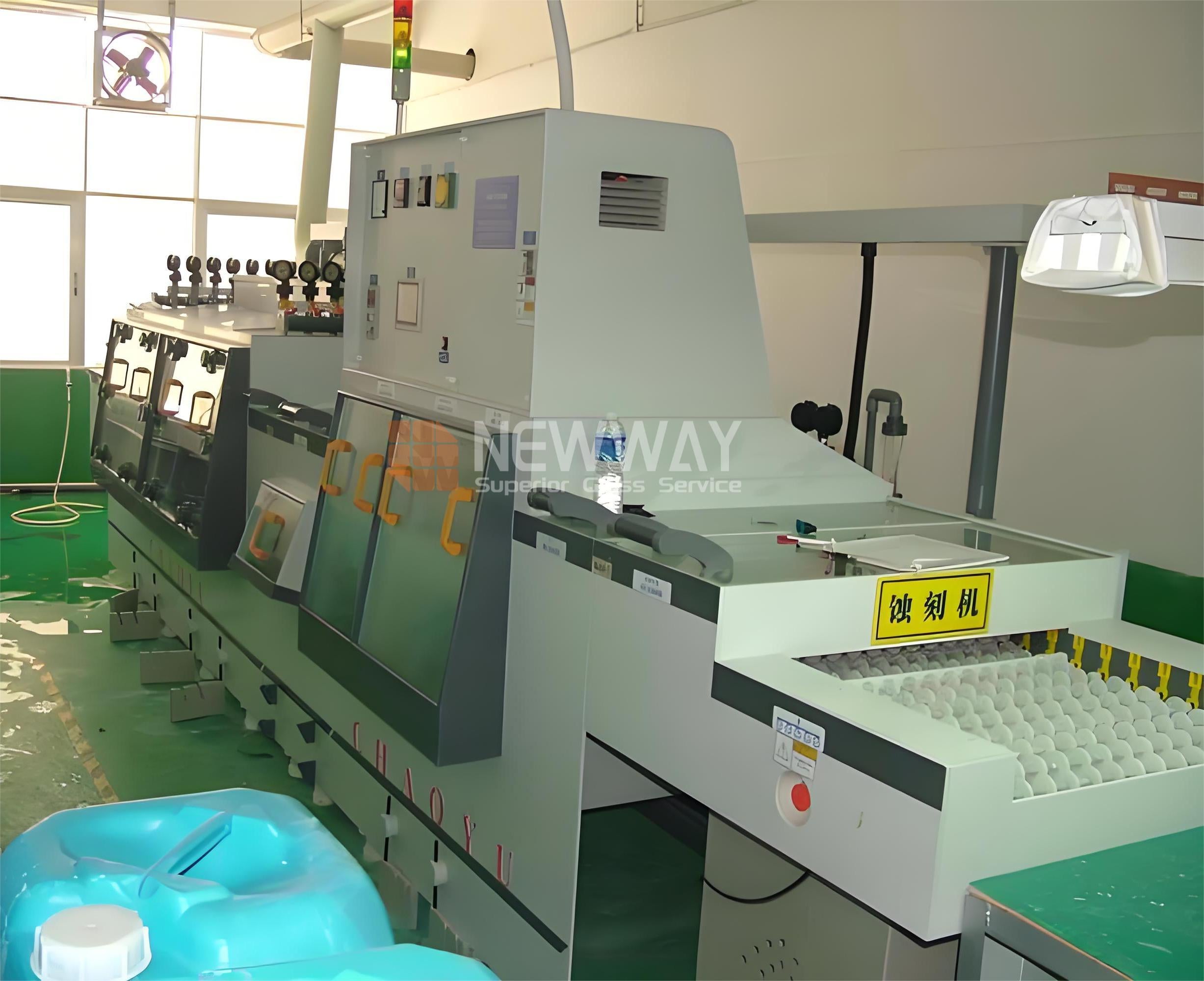
Chemical Etching AG
NWG's Chemical etching AG is a process by using the chemical reactions (mainly hydrofluoric acid) to turn the glass surfaces from flat surface into matte diffuse reflection surface. This method involves selectively removing material from the glass through the application of chemicals, resulting in a textured or frosted appearance that helps reduce reflections and glare.
Features of Chemical Etching AG
1.Complex Process
The ionization balance, chemical reactions, dissolution, recrystallization, ion replacement, and other reactions together, the AG effect, and particle size and shape by the reactant's composition and concentration, reaction time, temperature, and other factors make up the more complex process principle. The production is challenging and involves a high level of technology.
2.Uniform Texture
Chemical etching provides a uniform and controlled texture across the entire glass surface. This consistency ensures uniform anti-glare properties and enhances the overall aesthetic appeal.
3.Durability and Longevity
The anti-glare texture created through chemical etching is permanent and durable. It does not wear off over time, ensuring long-lasting performance.
Best choice for outdoor applications.
4.Flexibility
Any cold processing, including cutting and grinding, tempering, and other procedures, can be used on Etched AG glass without affecting the AG performance.
5.Environmentally Friendly
Etched AG layer doesn't contain volatile substances.
6.Higher Cost
With the use of higher standard and complex chemical agent and complex processes, as well as the reduction in production efficiency, has led to higher cost than Spraying AG.
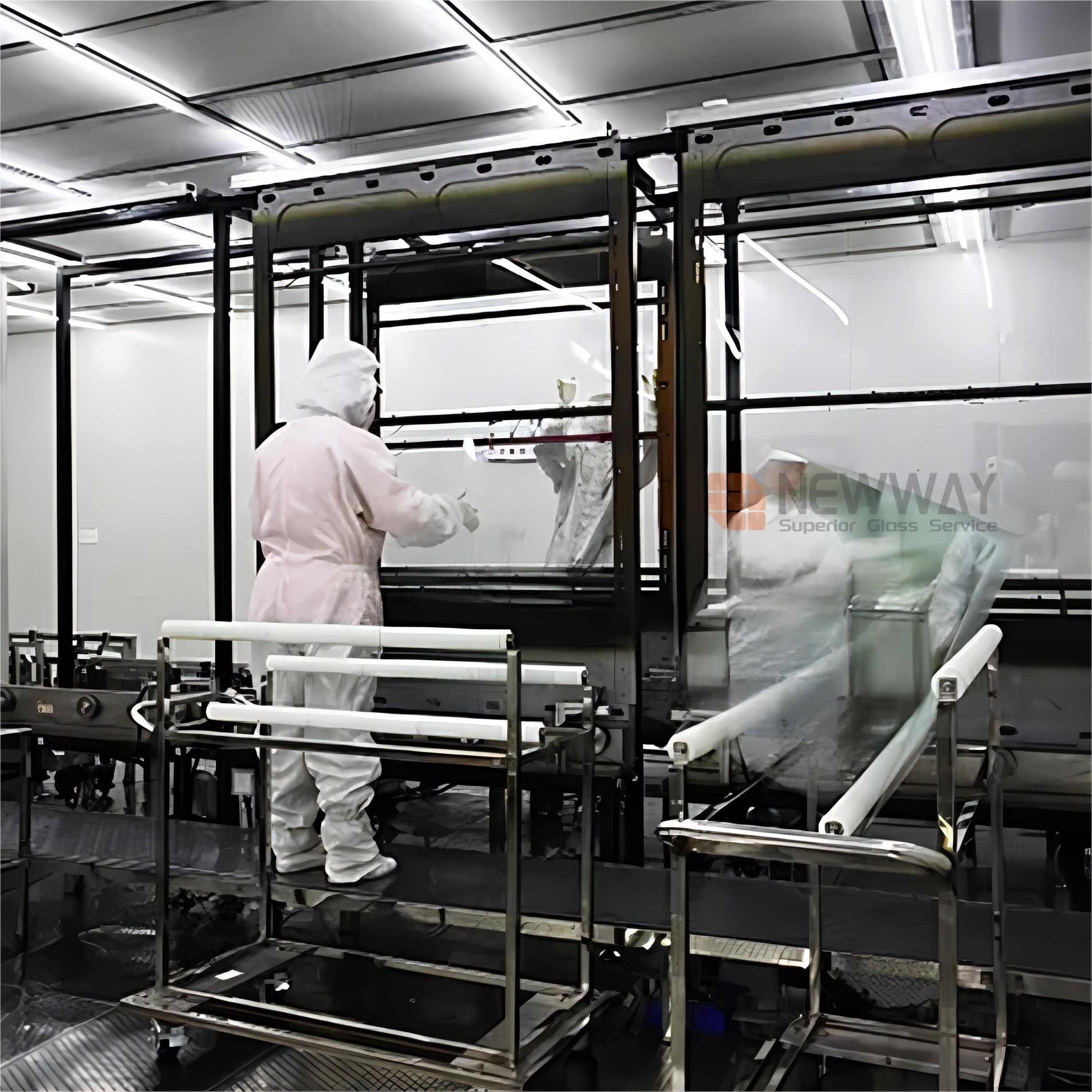
Spraying AG
Spraying AG is applied using a gun or disc atomizer, pressure, or centrifugal force to evenly coat the glass's surface with sub-micron silica and other particles. After the glass is heated and cured, a layer of particles forms on the surface, causing diffuse light reflection that creates the anti-glare effect.
Features of spraying AG
1.Simple Process
This process is convenient and fast. The AG (anti-glare) liquid is sprayed directly onto the glass surface to form AG layer, no pretreatment is necessary for the liquid. Easy to produce different haze and gloss glass products according to customer's requirements.
2.Uniform Coating Distribution
Spraying allows for even and consistent coverage of the AG coating across the entire glass surface. This helps in achieving uniform anti-glare properties.
3.Cost-Effective
Spraying AG coating typically requires less specialized equipment compared to Etching AG. This can result in cost savings.
4.Hardness
6-9H